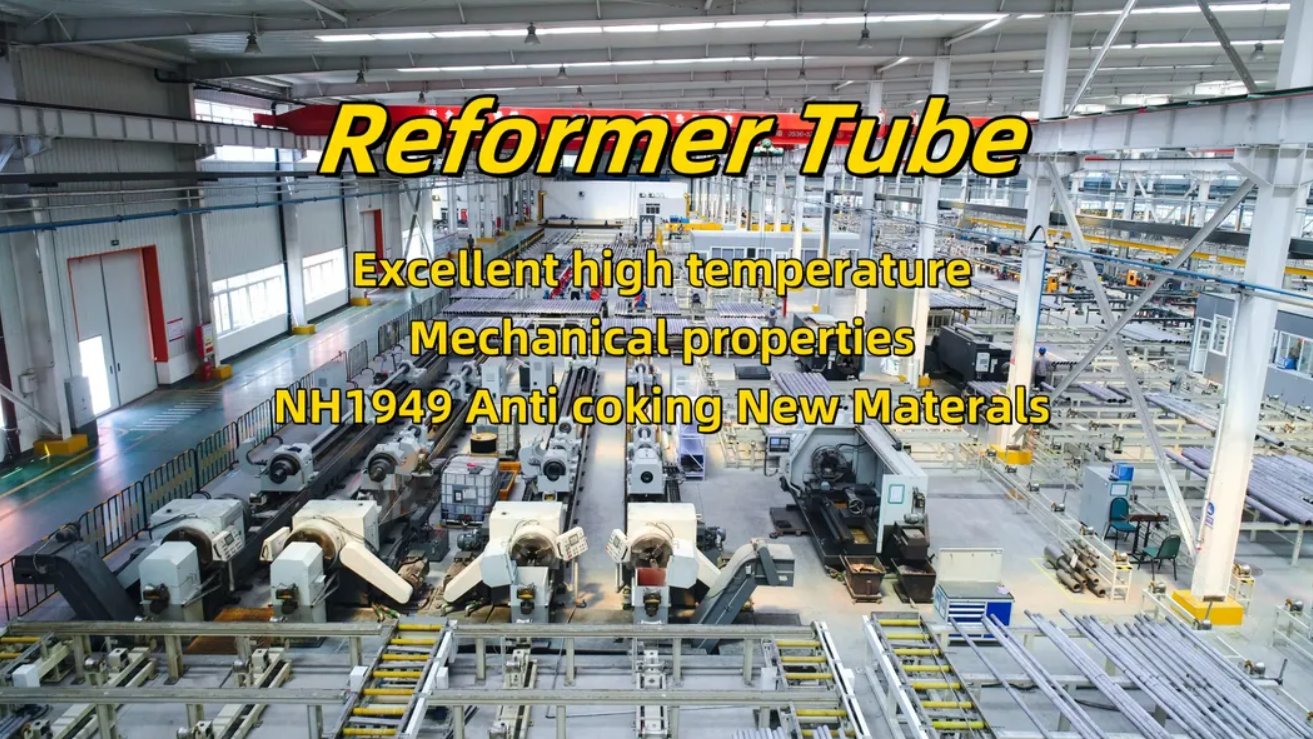
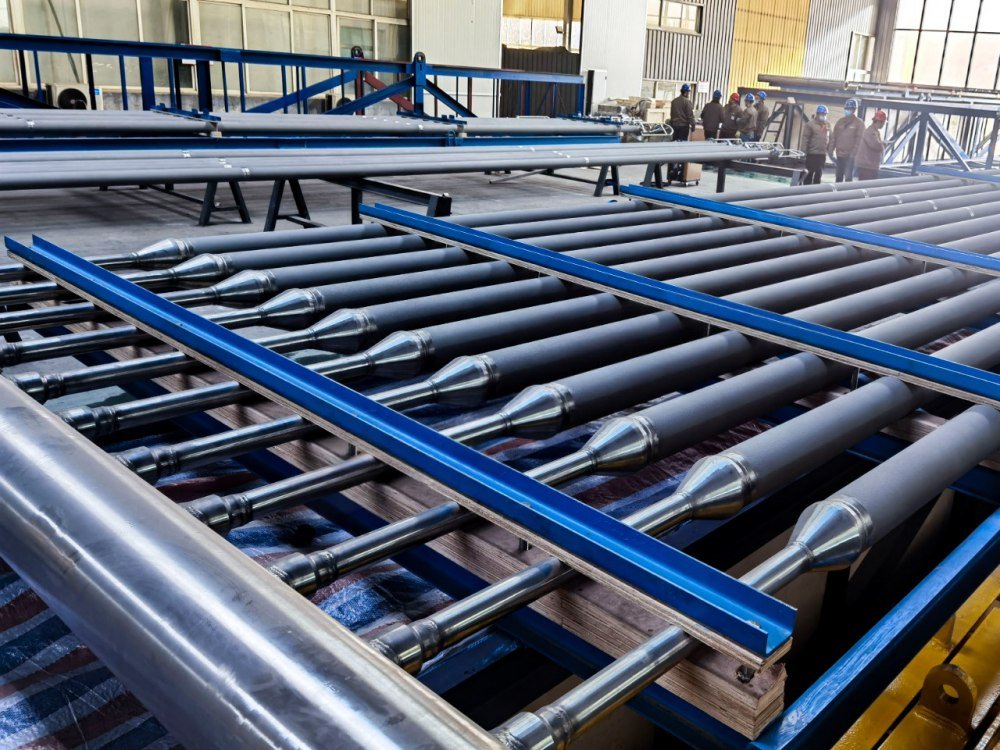
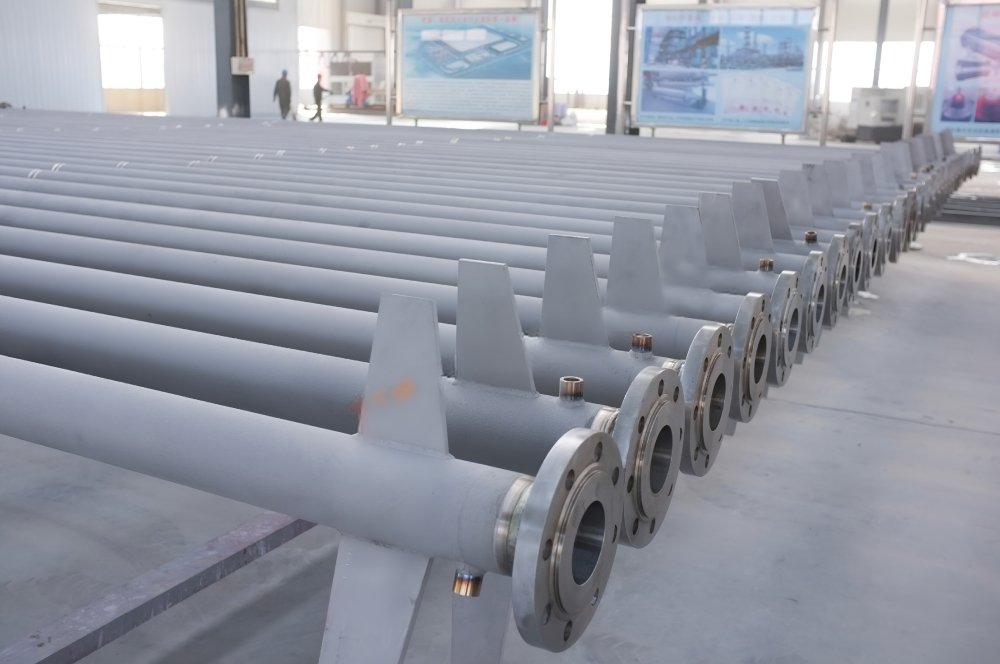
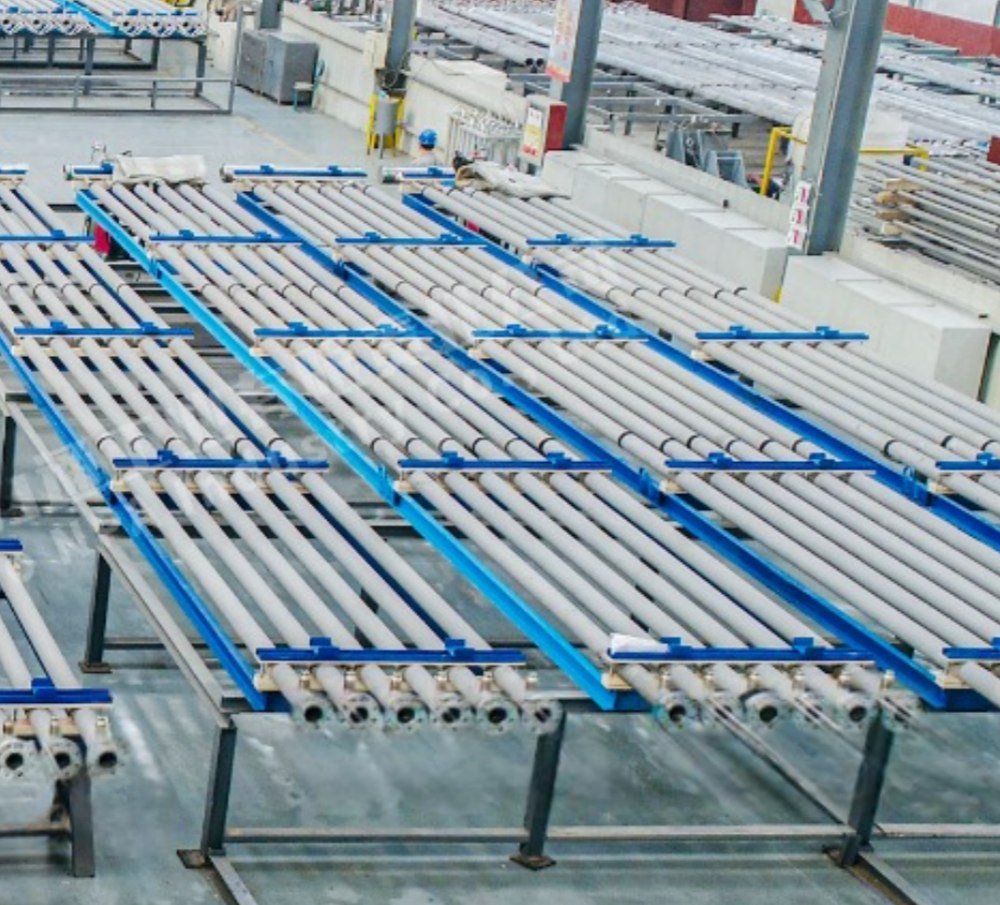
At the same time, it also has important applications in the production process of fertilizer synthesis ammonia and methanol production industry. The key equipment of the synthesis ammonia device is a primary converter, which provides the required raw gas hydrogen for the synthesis ammonia production of the fertilizer plant.
Product parameters:
★Working condition: 800-980ºC
★Operating Pressure: 2.5-3.5M
★ PaOuter diameter: 100-300mm
★ (Pipe section) length: <6400mm
★ Inner wall finish: Ra<3.2um (internal control 1.6um)
★ Bayberry particle layer: ≤0.8mm
Reformer tubes possess a suite of remarkable product characteristics that make them indispensable in their application domains.
High Temperature Endurance is a standout feature. These tubes are engineered to operate under extreme thermal conditions, routinely withstanding temperatures that can soar well above 800°C. This is made possible by the utilization of advanced high-temperature alloys, typically nickel-based, which maintain the tube's structural integrity and prevent deformation or softening even during prolonged exposure to intense heat.
Exceptional Corrosion Resistance is equally vital. In the harsh chemical environments they inhabit, reformer tubes come into contact with a variety of corrosive substances such as hydrogen sulfide and carbon dioxide. Their specially formulated alloy compositions and surface treatments act as a shield, effectively fending off corrosion and safeguarding the tube's longevity, ensuring reliable performance over an extended period.
Superior Heat Transfer Efficiency plays a crucial role in optimizing the overall process. The tube design and material selection are fine-tuned to facilitate rapid and uniform heat distribution throughout the reaction zone. This enables the reactions occurring within the tubes to proceed at an ideal rate, enhancing productivity and minimizing energy waste.
Robust Structural Integrity is another key aspect. They must endure significant mechanical stresses, not only from the high internal pressures generated by the reacting gases but also from thermal expansion and contraction cycles. Reformer tubes are built with sufficient strength and toughness to withstand these forces without succumbing to cracks, fractures, or other forms of damage.