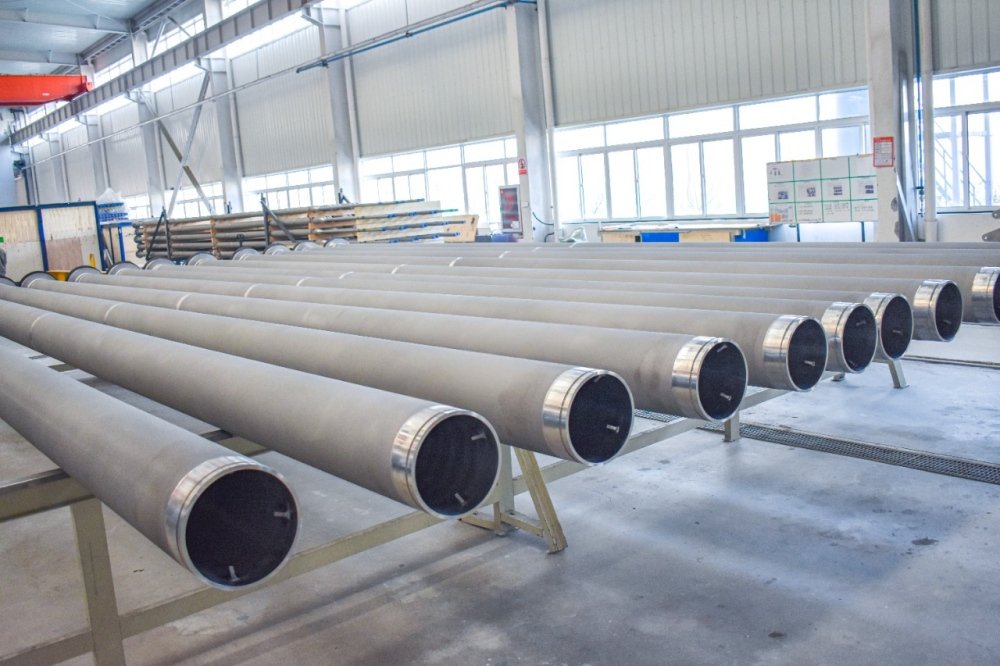
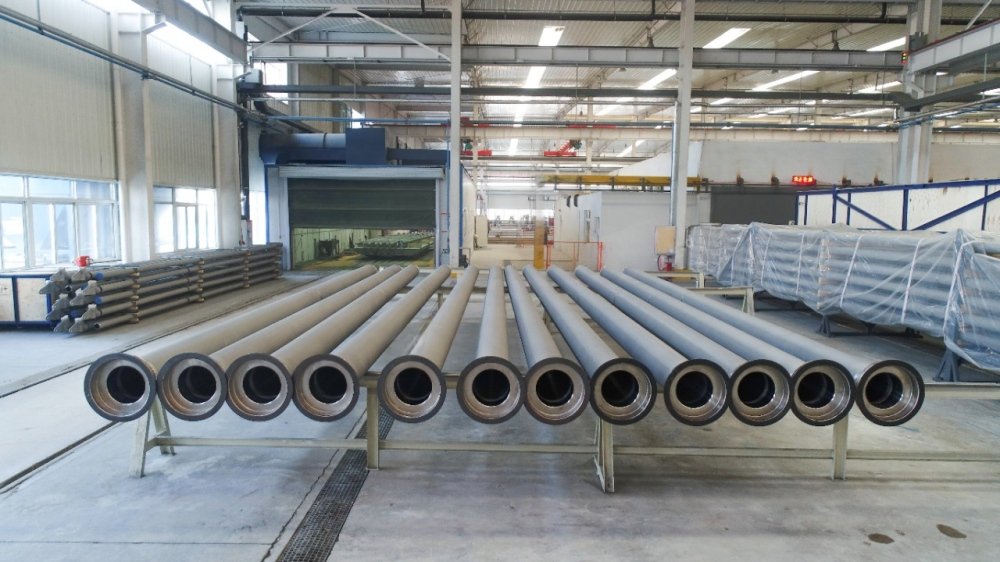
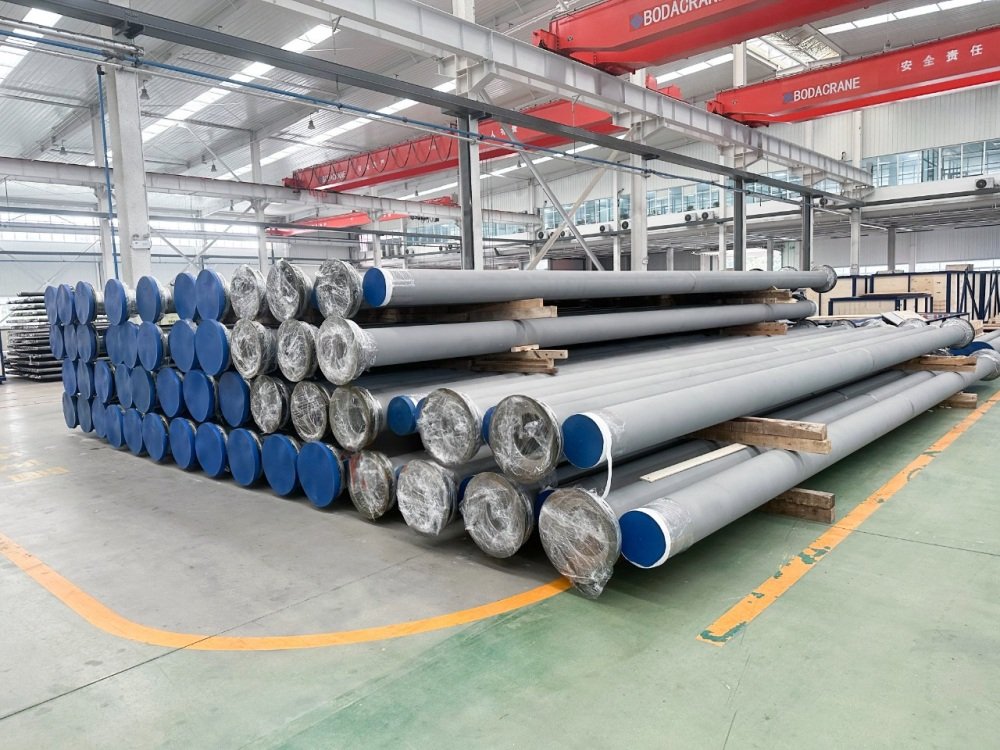
Technical Index:
Working condition: 800-1200℃,operating pressure 0.5-2MPa
Outer diameter: 90-300mm
(Pipe section)length: ≤6400mm
Inner wall finish: Ra≤3.2 μm (internal control 1.6μm)
Bayberry particle layer: ≤0.8mm
Service life: 8 years
Direct Reduced Iron DRI Tubes, also known as direct reduction process tubes, possess several notable product characteristics that are crucial for their performance in the direct reduction of iron ore. Here is a detailed introduction:
High Temperature Resistance: DRI Tubes are designed to endure high temperatures ranging from 800°C to 1200°C. This is achieved through the use of high - quality alloy steels, such as chromium - nickel - molybdenum alloys, which provide excellent thermal stability and prevent the tubes from deforming or melting under extreme heat.
Corrosion Resistance: In the direct reduction process, DRI Tubes are exposed to a variety of corrosive gases and substances, including carbon monoxide, hydrogen, and sulfur - containing gases. To combat this, the tubes are equipped with a special anti - corrosion coating or made from corrosion - resistant materials. This ensures their durability and extends their service life, even in harsh chemical environments.
Wear Resistance: The interior of DRI Tubes often comes into contact with solid particles, such as iron ore and reducing agents, which can cause wear and tear. To address this, the tubes are designed with a smooth inner surface and enhanced wear - resistant properties. This helps to maintain the integrity of the tube and prevent premature failure due to abrasion.
Good Thermal Conductivity: Efficient heat transfer is essential for the direct reduction process. DRI Tubes are made from materials with good thermal conductivity, allowing for rapid and uniform heat distribution throughout the tube. This ensures that the reduction reaction proceeds smoothly and efficiently, improving the quality and yield of DRI.
High Strength and Pressure Resistance: DRI Tubes need to withstand high internal pressures generated during the direct reduction process. They are engineered to have high strength and pressure - resistant capabilities, ensuring that they can safely contain the reacting gases and materials without leaking or bursting.
Dimensional Stability: Maintaining precise dimensions is crucial for the proper functioning of DRI Tubes. They are manufactured with high precision to ensure dimensional stability, even under extreme temperature and pressure conditions. This allows for easy installation and integration into the direct reduction plant, and helps to optimize the overall process.