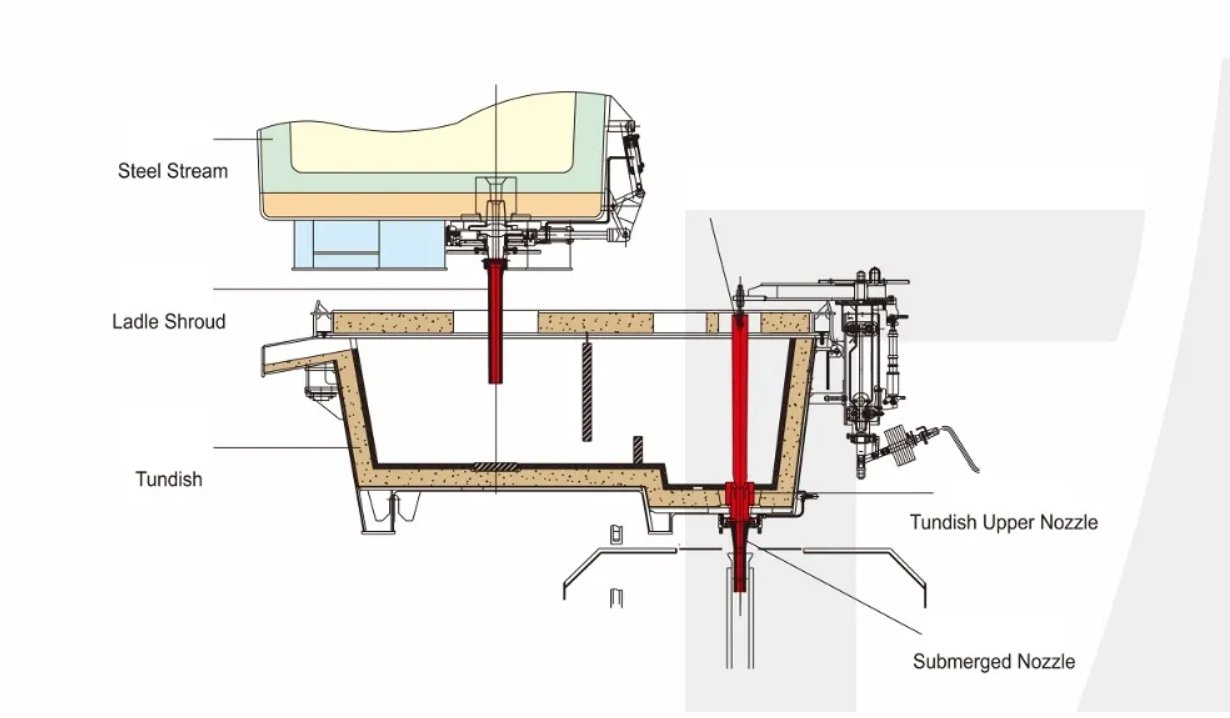
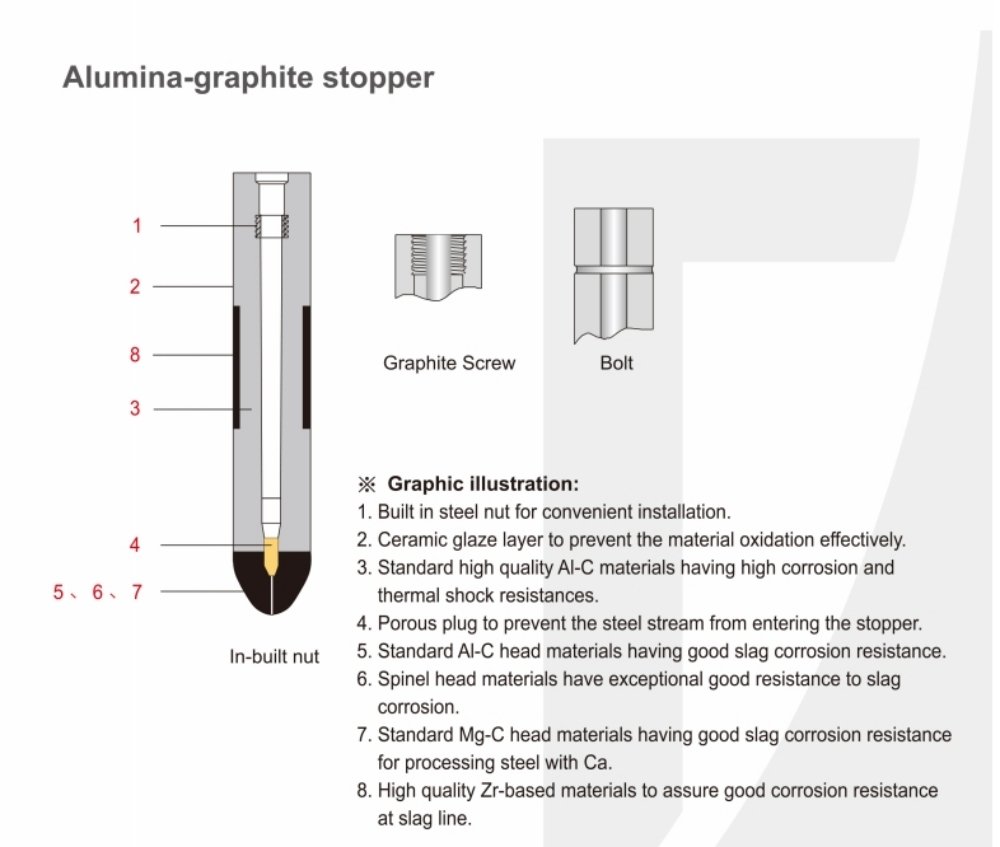
The Integral Stopper Rod comes with the following characteristics:
1. High Temperature Resistance
It is typically crafted from top - grade high - temperature. This enables it to withstand the high temperatures of molten steel during the continuous casting process. ensuring stable shape and performance in a long - term high - temperature environment.
2. Strong Erosion Resistance
As the stopper rod comes into direct contact with molten steel, it must possess excellent erosion resistance. Its material can resist the chemical corrosion and mechanical scouring of molten steel and slag. This guarantees the service life of the stopper rod, reduces the replacement frequency caused by erosion, and enhances the efficiency and stability of continuous casting production.
3. Good Thermal Stability
During the continuous casting process, the stopper rod experiences drastic temperature changes. Its good thermal stability allows it to withstand thermal shocks, making it less prone to cracking or spalling due to thermal stress. This ensures the structural integrity and performance reliability of the stopper rod.
4. Precise Flow Control
The head of the monolithic stopper rod is precisely designed. By cooperating with the nozzle, it can accurately control the flow of molten steel. Operators can flexibly adjust the position of the stopper rod according to the production process requirements, achieving precise regulation of the molten steel flow, thus guaranteeing the quality of the cast billet and the continuity of production.
5. High Strength and Rigidity
The stopper rod needs to remain stable under the static pressure and flowing impact force of molten steel. Therefore, it has high strength and rigidity. This allows the stopper rod to withstand large external forces without bending or breaking, ensuring normal operation during the continuous casting process and maintaining a stable flow of molten steel.
6. Overall Structural Reliability
The monolithic design eliminates potential problems such as loosening at the connection parts and molten steel leakage that may occur with split - type stopper rods. It enhances the overall reliability and sealing performance of the stopper rod. This structure can better meet the requirements of the continuous casting process and reduces production accidents and quality issues caused by stopper rod failures.