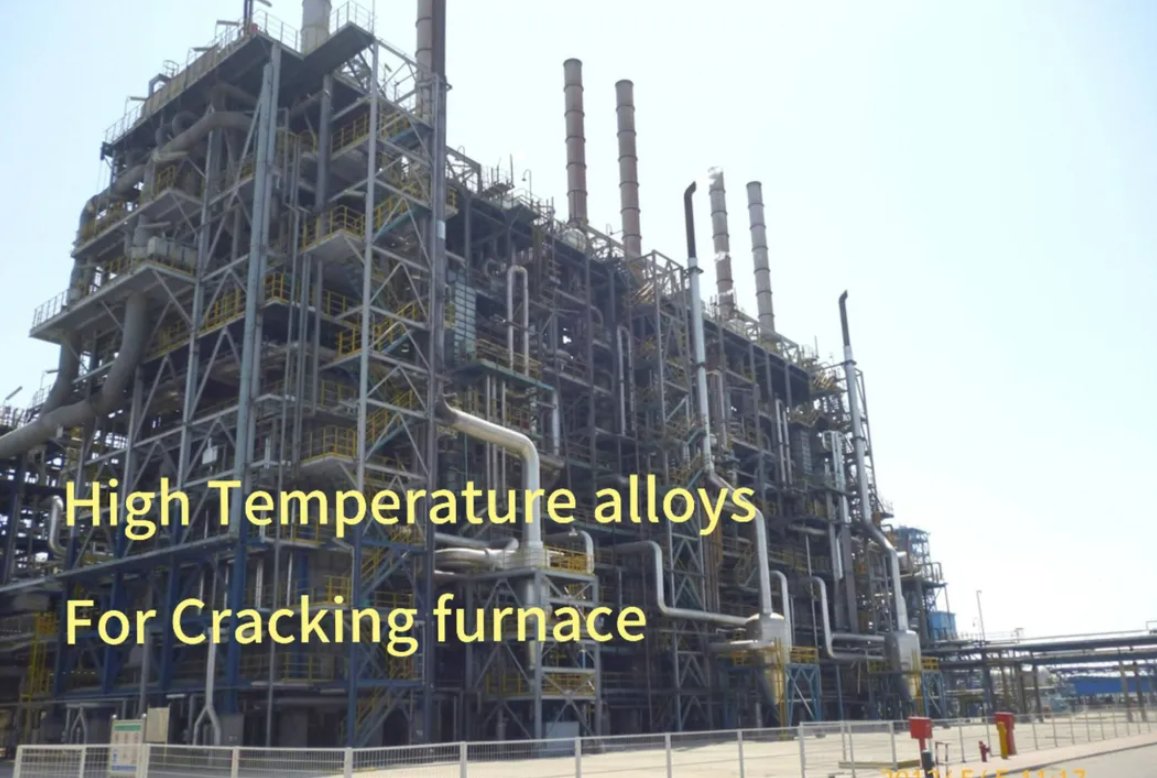
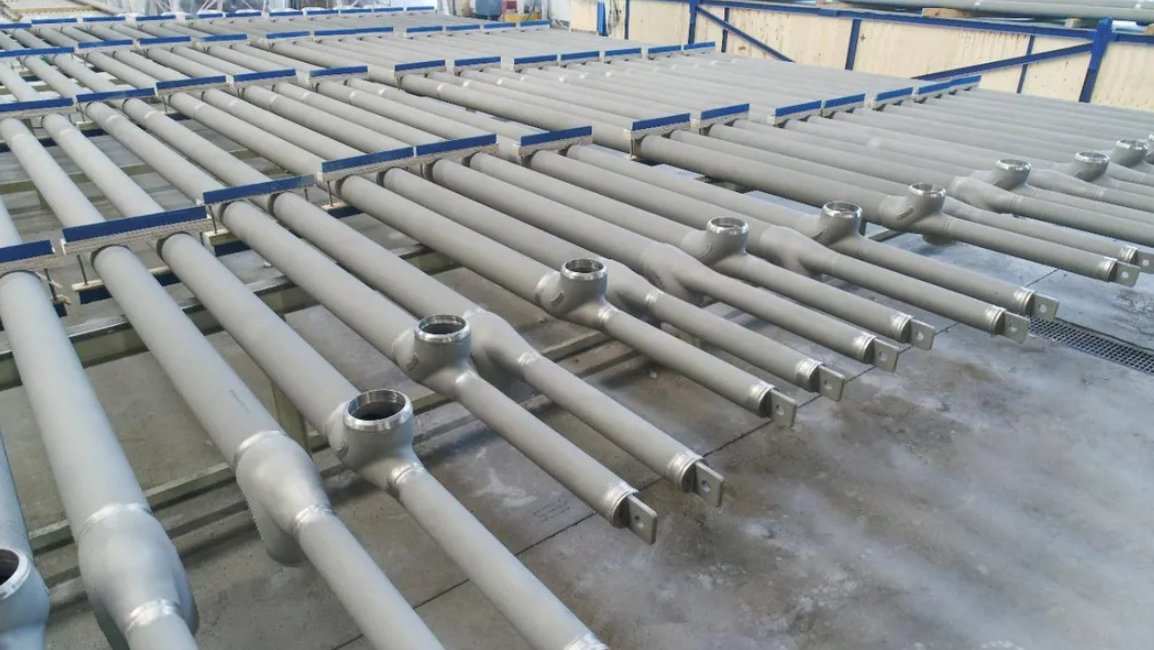
The cracking furnace coils, as a crucial equipment component in the petrochemical field, possesses a series of unique and outstanding product characteristics.
Firstly, it features high temperature resistance. During the cracking reaction process, the tube coil needs to endure extremely high temperatures ranging from 800°C to 1000°C or even higher for a long period. This demands the use of alloy materials with extremely strong high temperature resistance, such as nickel-based alloys and chromium-nickel alloys, to ensure structural stability under extreme heat without softening or deforming, thus maintaining the continuous and efficient progress of the cracking reaction.
Its anti-coking property is also remarkable. In the cracking process, coke is highly likely to adhere to the inner wall of the furnace tube. However, thanks to special surface treatment technologies like coating treatment or microstructure optimization, the tube coil reduces the adhesion force between reactants and the tube wall, minimizing coke formation. Even if a small amount of coke is generated, it can be easily removed through online decoking methods, effectively prolonging the operation cycle.
High strength and high toughness are equally important characteristics. When the cracking furnace is in operation, the tube coil not only has to withstand the impact of high-temperature and high-pressure media inside but also cope with stress changes caused by thermal expansion and contraction. Therefore, it has high strength to resist strong external impacts and prevent rupture. At the same time, it also has high toughness to adapt to frequent stress fluctuations and avoid brittle fracture, ensuring safe and reliable production.
Good thermal conductivity is indispensable for the cracking furnace tube coil. The rapid and uniform transfer of heat to the materials inside the tube is the key to improving cracking efficiency and reducing energy consumption. The special alloy materials it employs and the optimized tube coil structure significantly enhance the thermal conductivity efficiency, ensuring that the cracking reaction takes place in an ideal thermal environment.
Moreover, it has excellent corrosion resistance. The cracking process involves multiple corrosive media, such as hydrogen sulfide and sulfur dioxide. Through special alloy composition design and the addition of anti-corrosion coatings, the tube coil effectively resists the erosion of these media, extends its service life, reduces maintenance costs, and facilitates the long-term and stable operation of petrochemical enterprises.