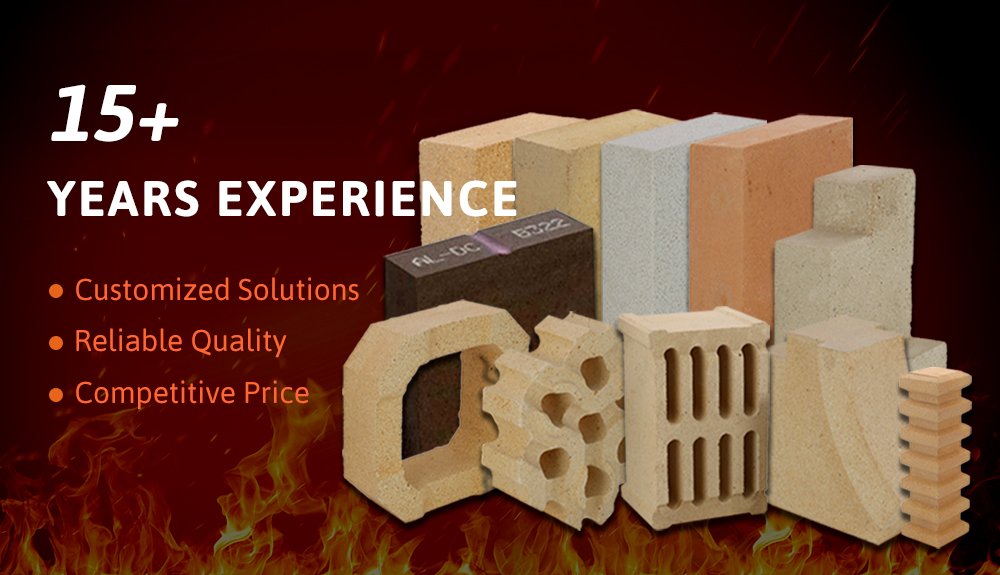
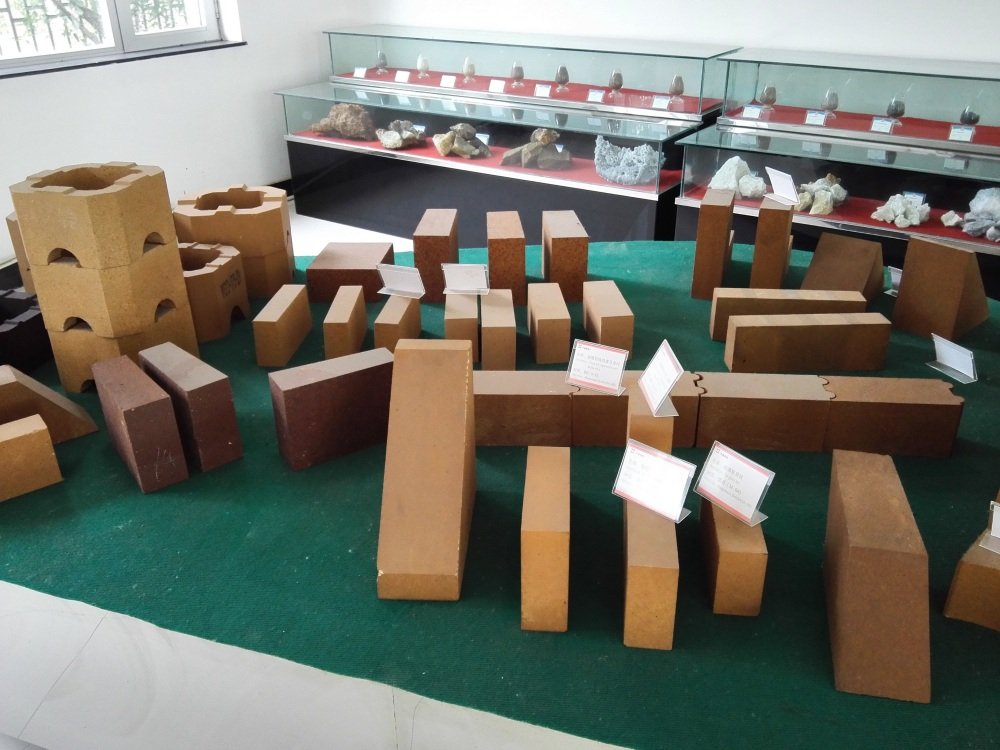
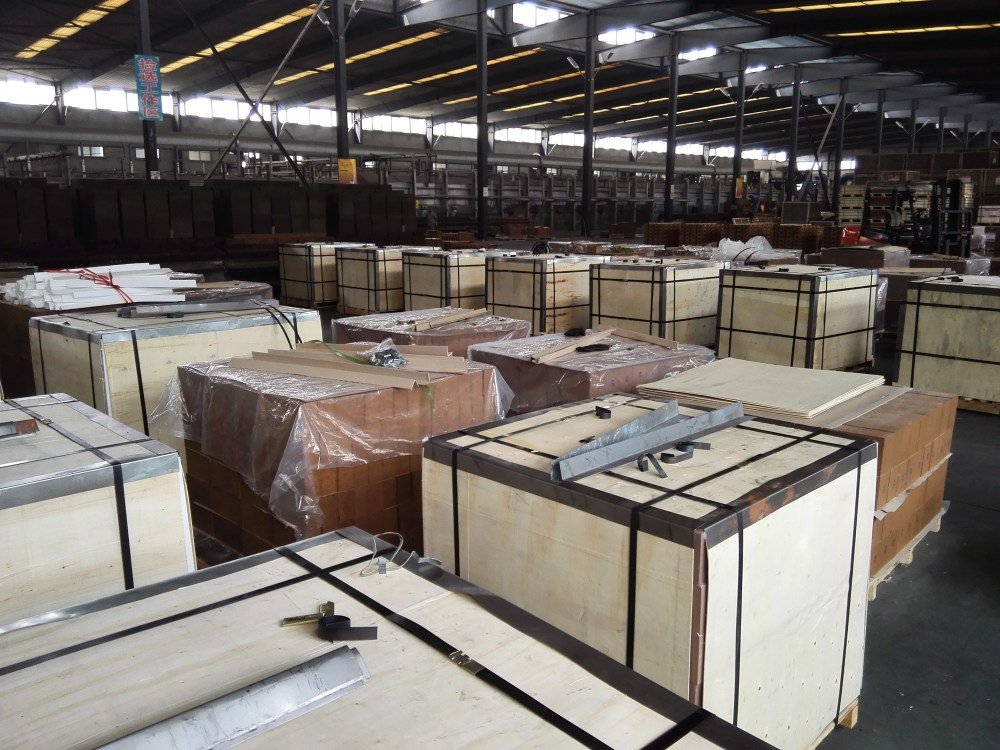
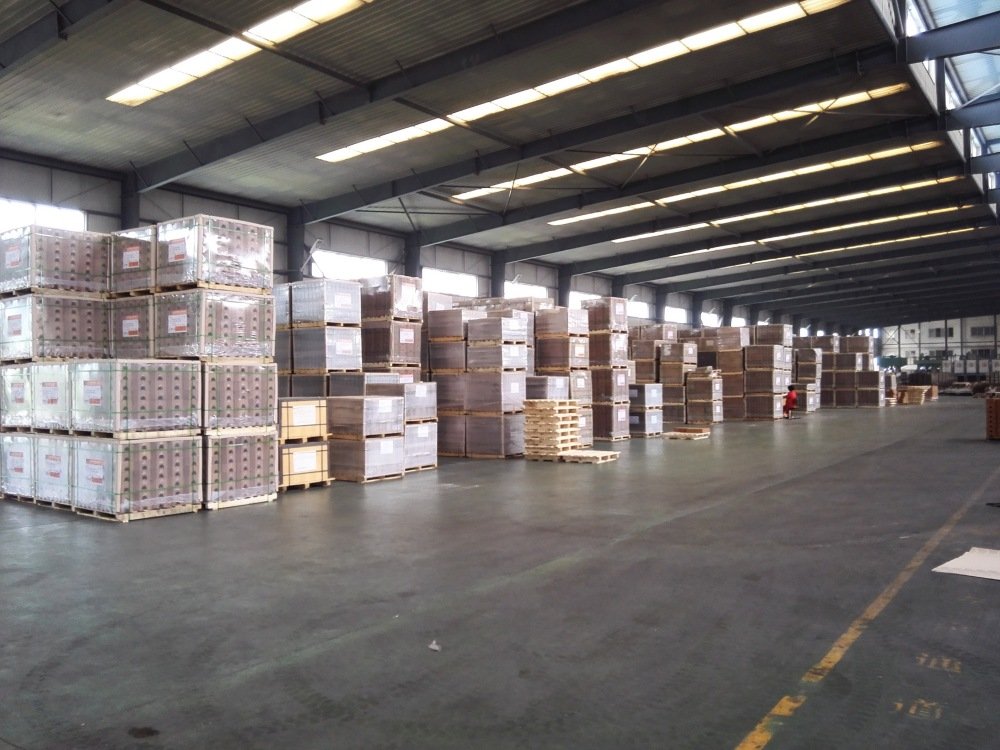
Magnesium aluminum spinel bricks possess the following remarkable characteristics:
1. Outstanding High-Temperature Resistance: The spinel structure formed by its main components has an extremely high melting point, enabling it to endure long-term high-temperature exposure in high-temperature furnaces with ease. It remains structurally stable even in extremely high-temperature environments and is not prone to softening or deformation, providing reliable support for high-temperature operations.
2. Excellent Thermal Shock Stability: It has a relatively low coefficient of thermal expansion, which allows it to effectively buffer thermal stress when facing frequent furnace start-ups and shutdowns, as well as rapid temperature fluctuations. This significantly reduces the risks of cracking and spalling of the brick body, ensuring the continuity and stability of production.
3. Strong Chemical Corrosion Resistance: It has relatively stable chemical properties. Whether facing alkaline slag, acidic gases, or other corrosive media at high temperatures, it exhibits strong resistance, effectively preventing in-depth erosion and prolonging its service life, thus reducing maintenance costs.
4. High Mechanical Strength: It has high compressive and flexural strengths at room temperature and can also maintain good mechanical properties at high temperatures. It can withstand the heavy pressure of materials in the furnace, the scouring of gas flow, and mechanical collisions during the loading and unloading processes, ensuring the integrity of the furnace lining.
5. Good and Controllable Thermal Conductivity: On the one hand, it can conduct heat quickly, making the temperature distribution in the furnace more uniform, which is beneficial for process control. On the other hand, magnesium-aluminum spinel bricks prepared through special processes can also meet the need for low thermal conductivity, reducing heat loss from the furnace and achieving energy-saving purposes.