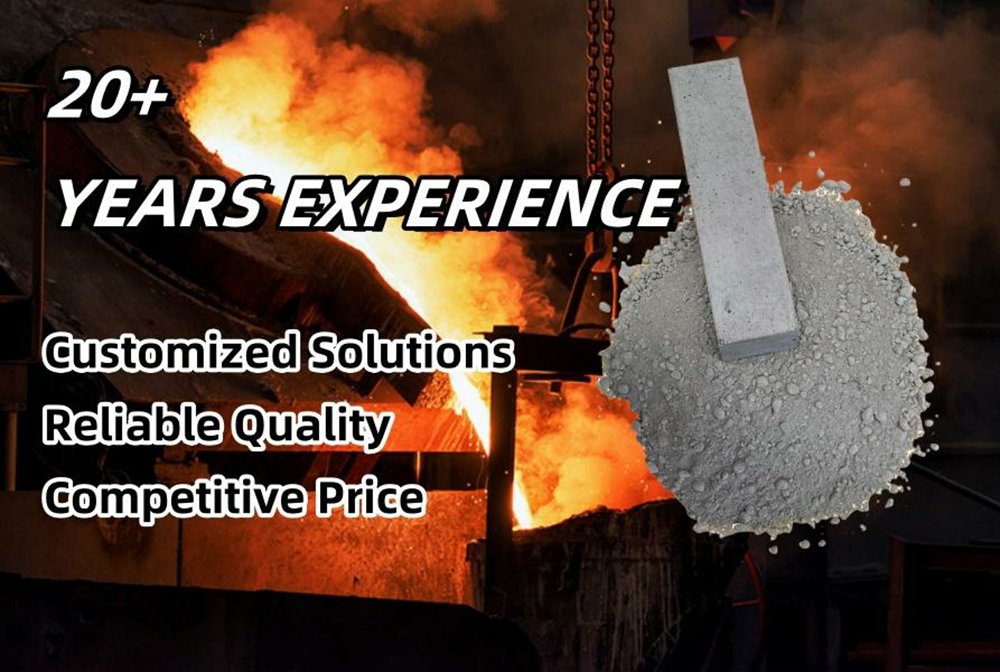
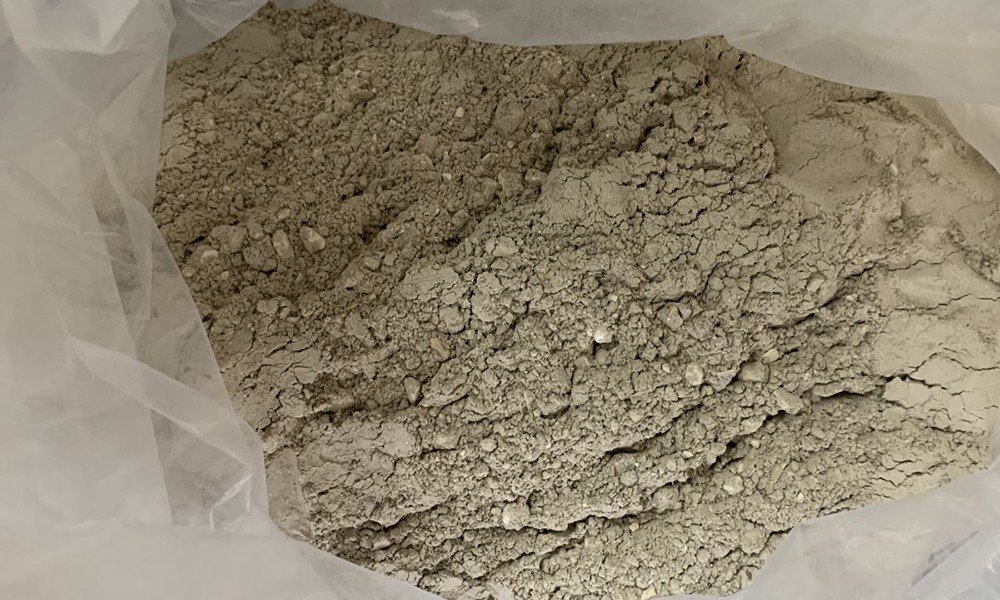
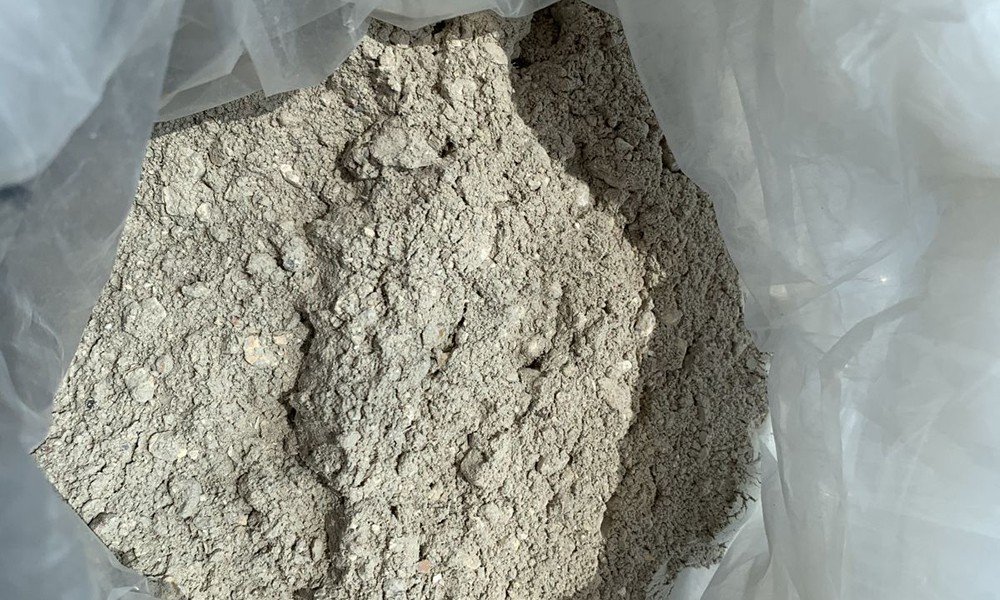
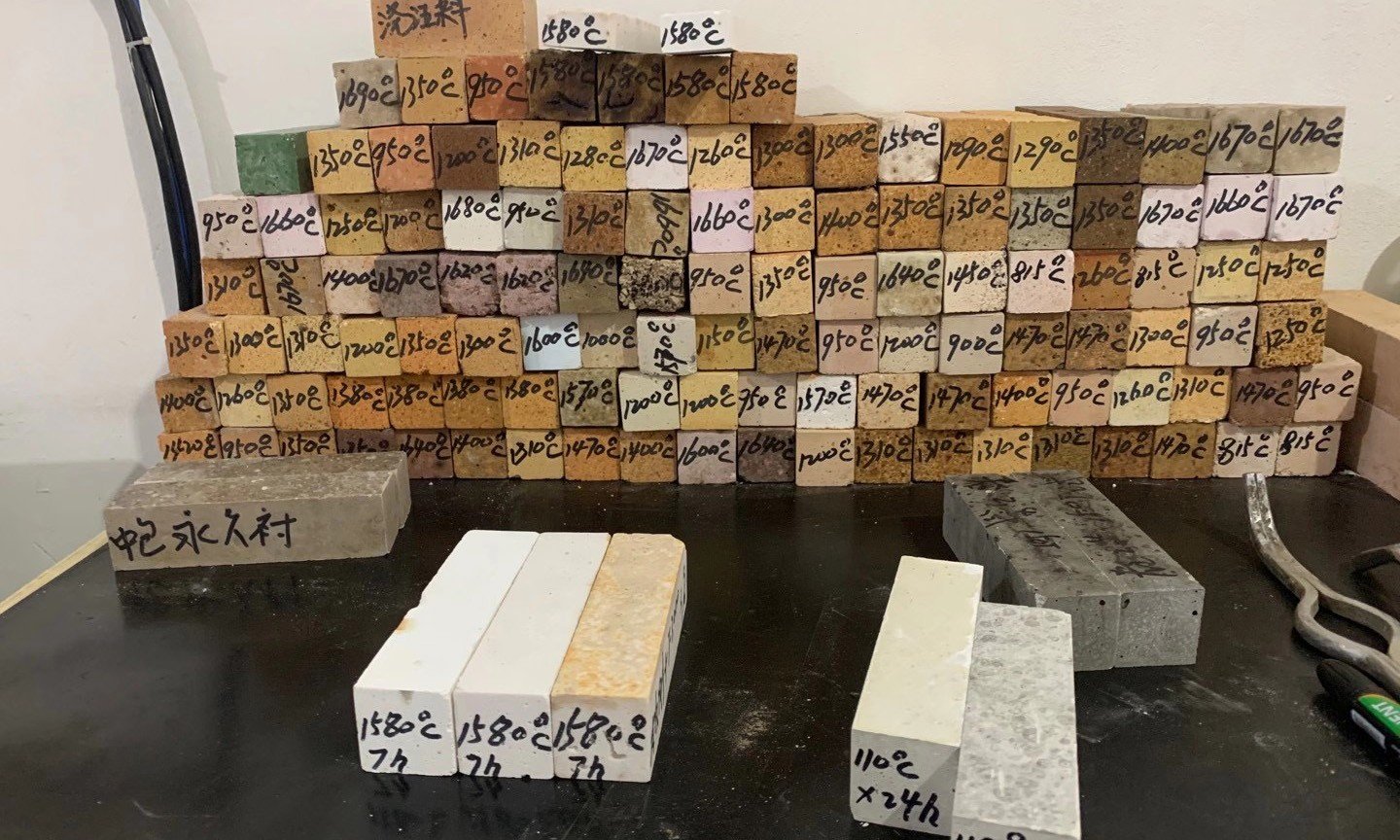
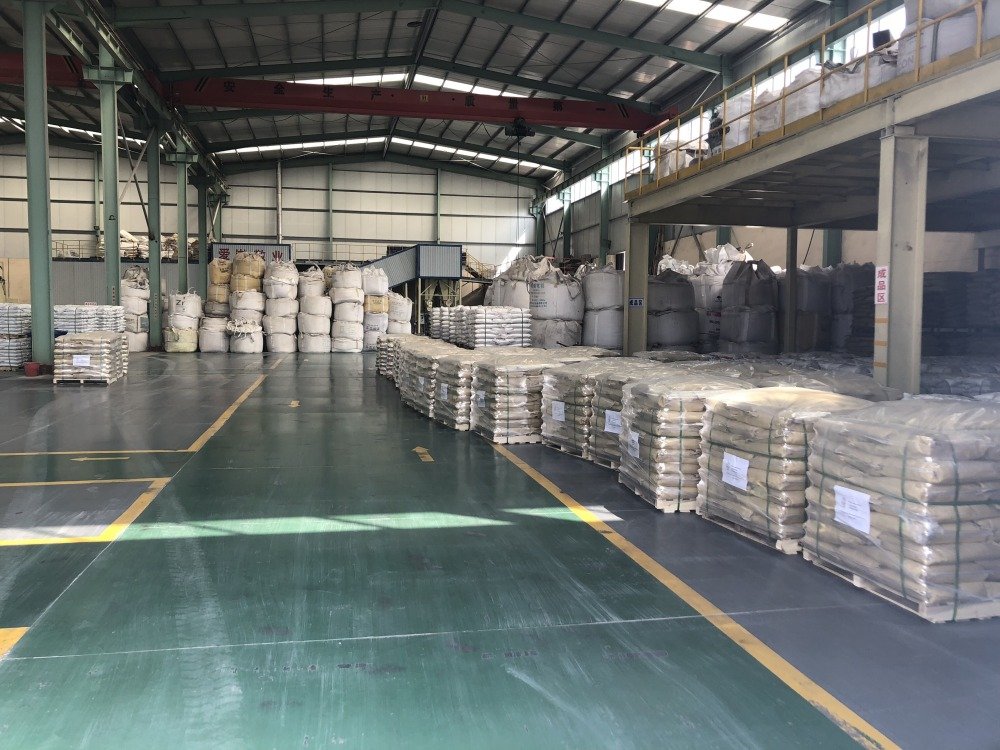
Refractory castables have the following characteristics:
Good fluidity: During construction, refractory castables such as refractory cement castable and plastic castable exhibit excellent fluidity, allowing them to quickly and evenly fill molds or construction areas. This characteristic ensures proper forming even in complex-shaped parts, greatly facilitating construction operations and significantly improving efficiency.
High refractoriness: Refractory castable materials possess outstanding resistance to high temperatures, typically ranging from 1580°C to 1770°C or even higher. This makes them suitable for various high-temperature industrial kilns and thermal equipment. Their structural stability under extreme heat prevents softening and deformation, ensuring reliable long-term performance.
Good thermal shock resistance: Both refractory castable and plastic castable are designed to withstand sudden temperature changes without damage. Their structural and compositional characteristics allow them to absorb thermal stress, minimizing the risk of cracking or spalling during rapid heating or cooling processes in kilns and other equipment, thus extending service life.
High abrasion resistance: With a dense structure and relatively high hardness, refractory cement castables maintain excellent abrasion resistance, even under high-temperature conditions. This makes them ideal for applications such as cement rotary kilns or ore roasting furnaces, where they endure intense material scouring and friction, reducing material wear and ensuring the continuous operation of equipment.
Good corrosion resistance: Refractory castables and refractory mortar offer good resistance to corrosive media, including furnace slag, molten metals, and corrosive gases. At high temperatures, certain components form a dense protective layer that resists chemical penetration and reactions, enhancing their durability in harsh environments.
Good integrity: Once cured, refractory castables form a seamless structure with no or minimal joints. This integrity helps eliminate issues such as heat leakage or gas channeling, which are common in jointed linings. It enhances the thermal insulation and sealing performance of kilns, reduces energy loss, and boosts overall structural stability.
Strong repairability: Unlike some shaped refractory products, refractory castable linings can be locally repaired if damaged. This feature reduces the need for full replacement, cutting down maintenance costs and equipment downtime, and improving production efficiency. Whether using plastic castable or refractory mortar for patching, repairs are efficient and cost-effective.