Refractory kiln furniture is a critical component in high-temperature industries. Common materials include silicon carbide (SiC), alumina, mullite, and cordierite, each selected for properties like heat resistance, corrosion resistance, low thermal expansion, or lightweight design. Key types include kiln posts (vertical support), shelves (horizontal load-bearing), saggars (contamination isolation), pusher plates (product transport), and setter plates (direct workpiece holding). These components are widely used in sintering ceramics, glass, and electronics, protecting products from extreme heat while enhancing energy efficiency through optimized kiln design, ensuring both process reliability and product quality.
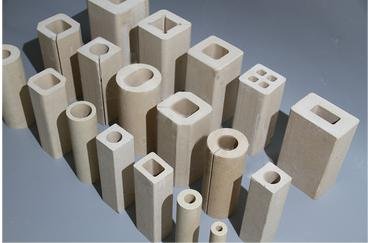
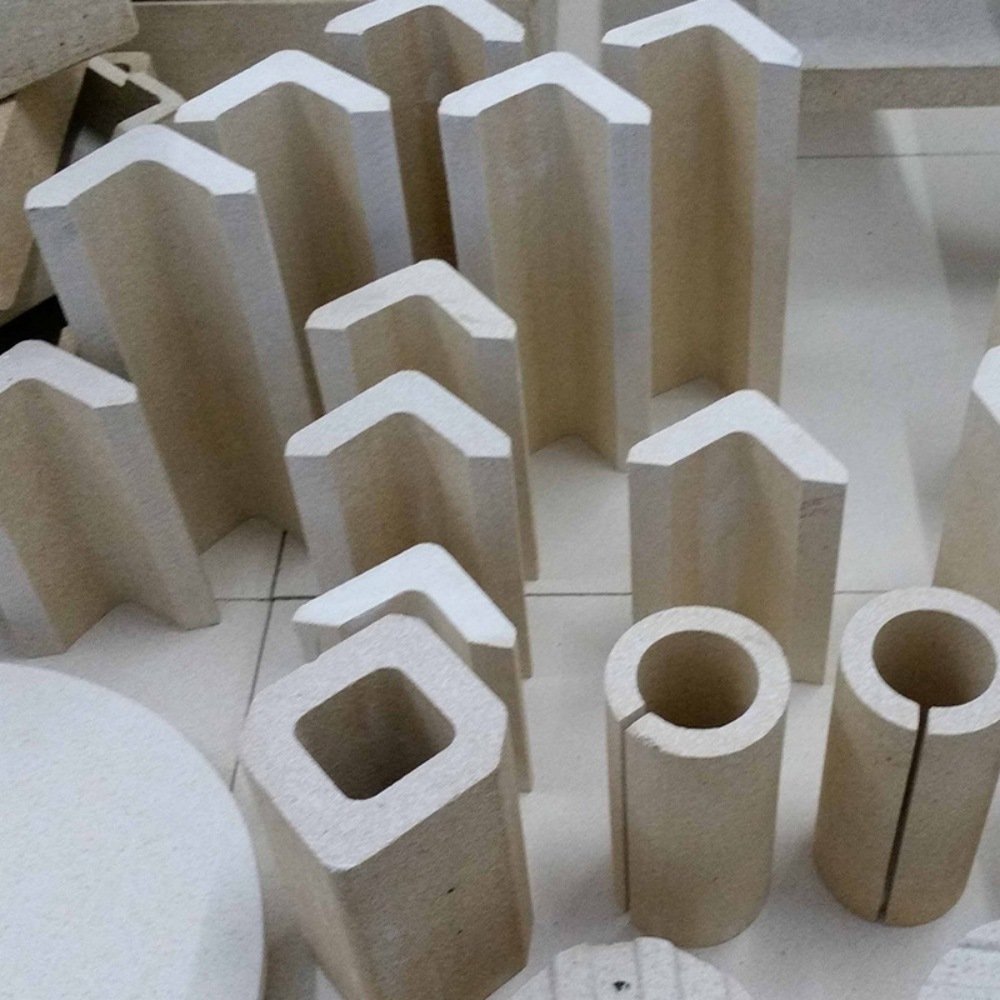
Extruded Props for kiln furniture possess numerous unique features that set them apart in the family of kiln tools.
In terms of structural design, the hollow structure is truly distinctive. Compared with solid pillars, it breaks the norm. The hollow interior acts like a natural heat insulation barrier, effectively preventing rapid heat conduction and significantly enhancing the thermal efficiency of the kiln, an advantage that solid pillars can hardly achieve.
Regarding material application, it is precisely matched with the hollow form. Not only must the outer shell material be high-temperature resistant and corrosion resistant to cope with the harsh environment inside the kiln, but the internal support structure also needs to have sufficient toughness to maintain overall stability. This composite material combination is specially customized for the special requirements of hollow pillars.
In terms of performance, its thermal stability is outstanding. When the kiln heats up and cools down, the thermal stress changes frequently. The hollow pillars, with the combined efforts of their structure and materials, quickly balance the stress generated by thermal expansion and contraction, eliminating the risks of cracks and deformation and ensuring the continuity of the firing process. This is far superior to ordinary pillars.
Moreover, the lightweight advantage is significant. During handling and installation, workers can easily manage them, reducing labor intensity and operation difficulty. At the same time, it relieves the load on the kiln bearing system, slowing down the structural wear under long-term heavy pressure and prolonging the service life of the kiln, saving equipment maintenance costs for enterprises.
Furthermore, the air permeability function is remarkable. Under specific designs, the air passage promotes the even flow of gases inside the kiln, optimizing the firing atmosphere, ensuring that products are heated and chemically reacted uniformly, and helping to produce exquisite products with uniform quality and pure color. It is an unsung hero in improving the quality of finished products.