Molybdenum Disilicide Heating Elements, also known as MoSi₂ rods, are outstanding heating components that are widely applied in high-temperature industrial scenarios. Composed mainly of molybdenum and silicon, these rods possess excellent high-temperature resistance capabilities. This makes them highly suitable for use in furnaces and kilns where extremely high temperatures are required, such as in the ceramic, glass, and metallurgical industries. Their unique structural design gives them good electrical conductivity, allowing for efficient conversion of electrical energy into heat. Moreover, molybdenum disilicide rods exhibit relatively stable chemical properties. They are resistant to oxidation and corrosion in harsh environments, ensuring a long service life and reliable performance. They significantly contribute to the smooth operation and productivity improvement of various industrial processes.
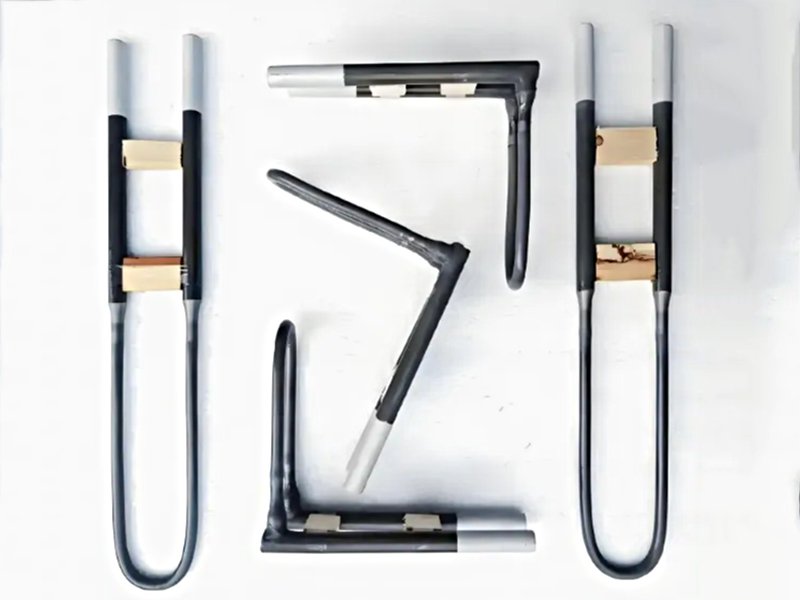
The following are the product characteristics of Molybdenum Disilicide Heating Elements (MoSi₂ Heating Elements):
Outstanding High-Temperature Resistance: Molybdenum Disilicide Heating Elements can operate stably in a high-temperature environment and withstand temperatures much higher than those tolerated by ordinary metal materials. They do not easily soften, deform or melt during long-term use in high-temperature furnaces, ensuring the continuous stability of the heating process.
Excellent Oxidation Resistance: In a high-temperature and oxygen-rich environment, a dense silicon dioxide protective film will form on the surface of Molybdenum Disilicide Heating Elements. This film effectively prevents the internal material from further oxidation and greatly extends their service life in a high-temperature oxidizing atmosphere.
High Electrothermal Conversion Efficiency: They possess good electrical conductivity. Once energized, they can quickly and efficiently convert electrical energy into heat, with a fast heating speed and high heating efficiency, enabling them to rapidly provide the required heat for industrial production.
Strong Chemical Stability: Besides oxidation resistance, Molybdenum Disilicide Heating Elements have relatively good tolerance to many chemical substances. They can maintain stable performance even in an environment with corrosive gases or chemica l media and are not prone to chemical reactions that lead to damage.
Relatively High Mechanical Strength: Although operating at high temperatures, Molybdenum Disilicide Heating Elements still have a certain degree of mechanical strength. They can bear a certain load and external force without easily breaking, ensuring stability during installation and use.
Good Resistance Stability: During use, the resistance value of Molybdenum Disilicide Heating Elements changes little and can maintain a relatively stable heating power, facilitating precise control of the heating temperature and ensuring the consistency of the production process and the stability of product quality.
Simple Installation and Maintenance: The structural design of Molybdenum Disilicide Heating Elements is reasonable, and the installation method is relatively simple. Moreover, due to their stable performance and long service life, the frequency and difficulty of daily maintenance are low, which can reduce the maintenance cost and downtime of the equipment.