
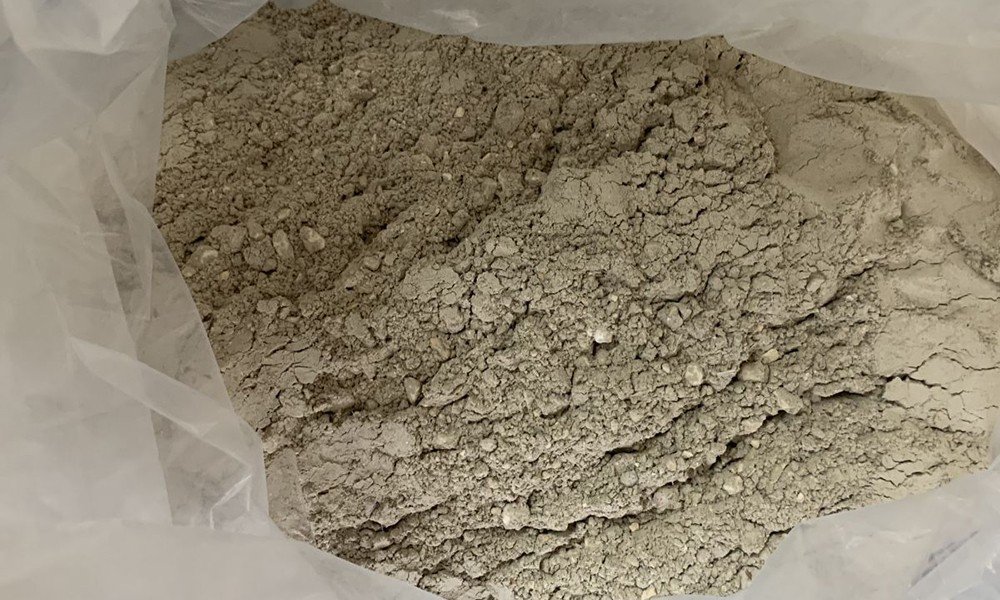
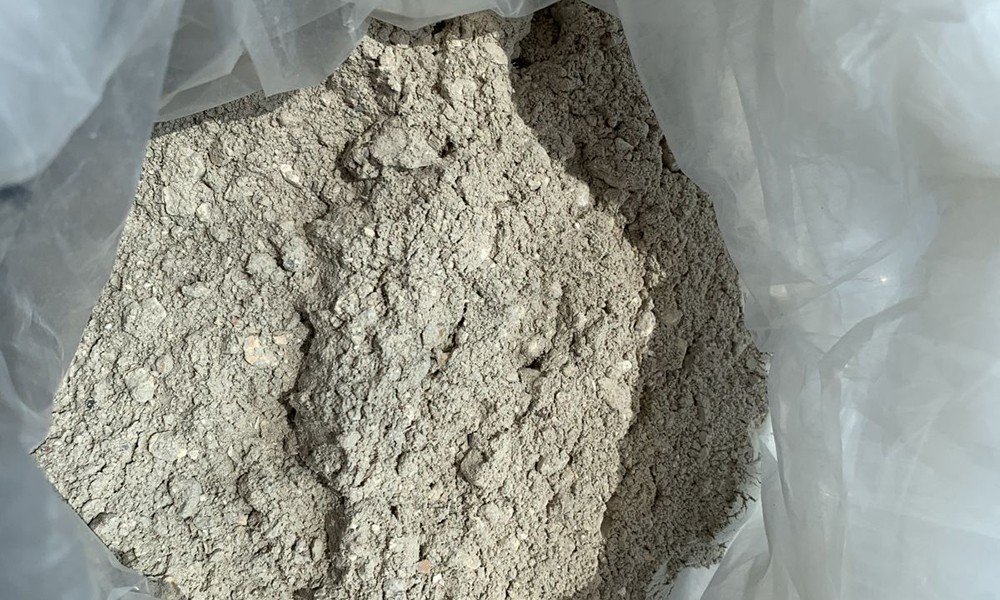
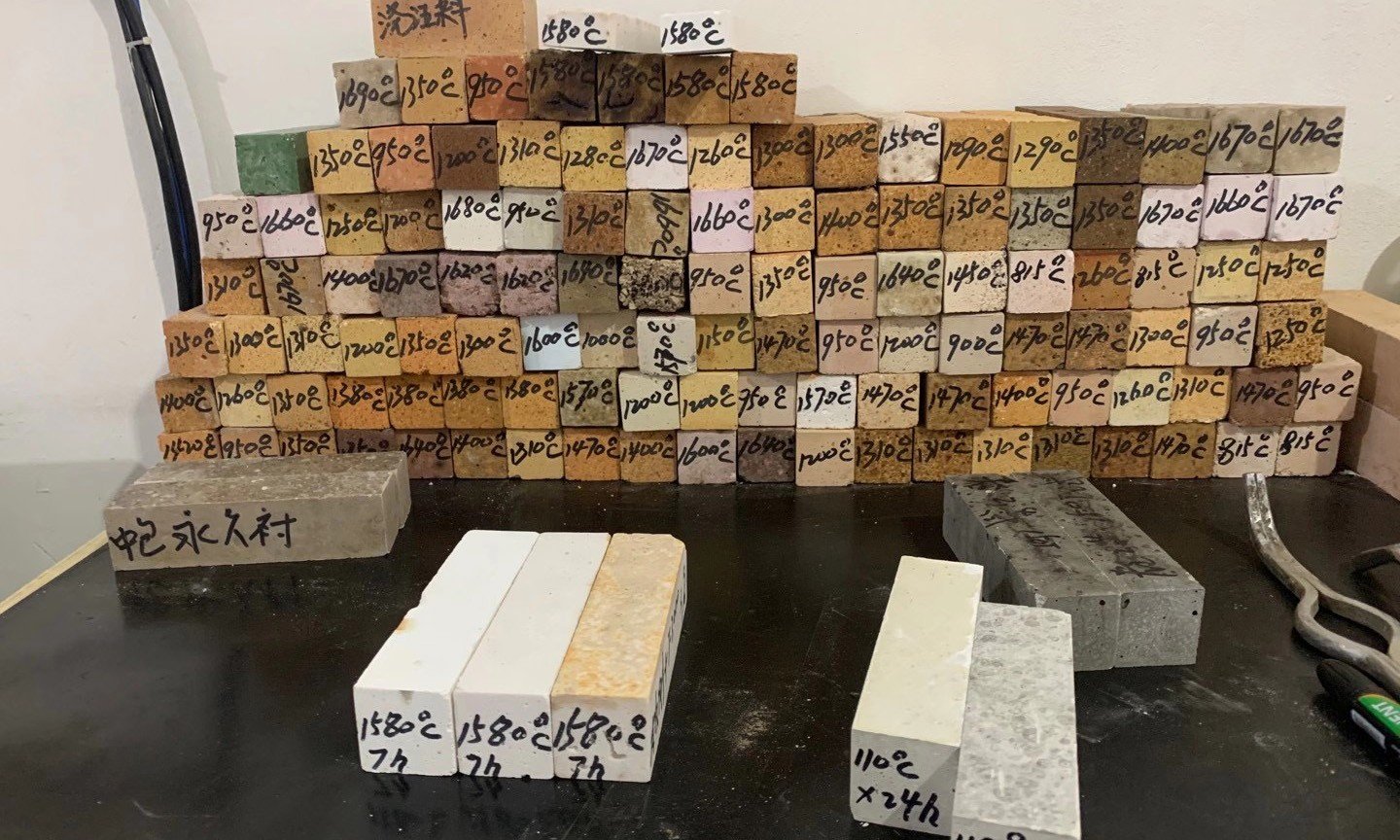
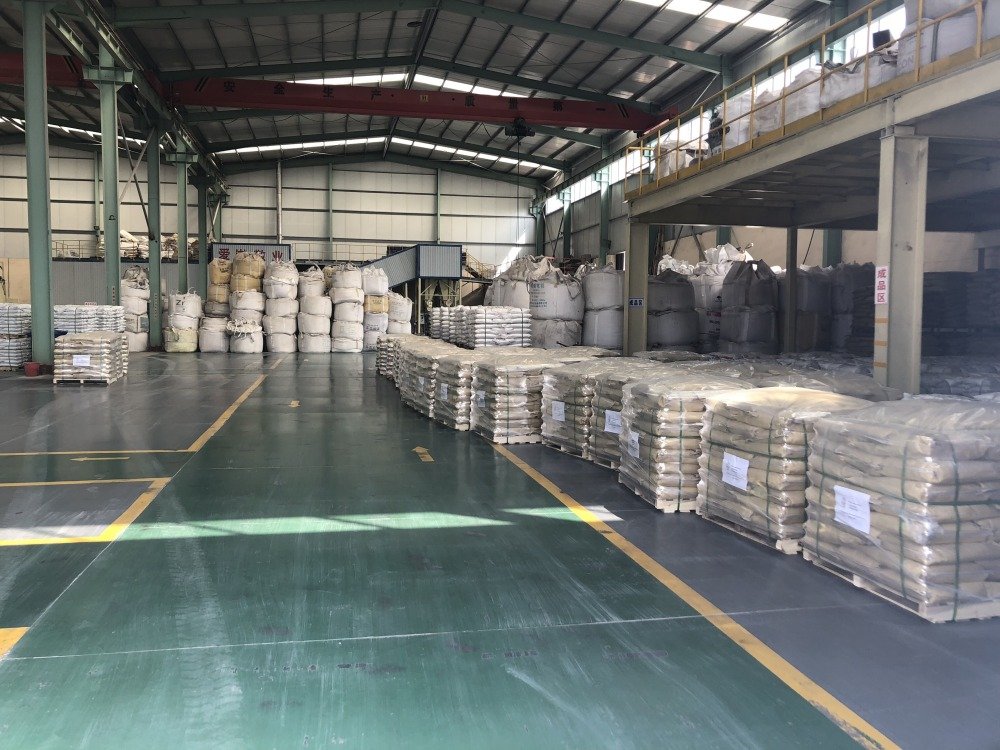
Refractory castables have the following characteristics:
1. Good fluidity: During construction, refractory castables exhibit fluidity similar to that of a fluid, enabling them to quickly and evenly fill molds or construction sites. They can be well formed even in parts with complex shapes, which facilitates construction operations and greatly improves construction efficiency.
2. High refractoriness: They are capable of withstanding high-temperature environments. Generally, the refractoriness can reach above 1580°C - 1770°C, and some are even higher. They can meet the usage requirements of different high-temperature industrial kilns and other thermal equipment, maintaining structural stability at high temperatures and being less likely to soften and deform.
3. Good thermal shock resistance: They possess a certain ability to resist sudden temperature changes without damage. When there are sudden temperature changes during the heating or cooling process of kilns and other equipment, refractory castables can buffer thermal stress through their own structural and compositional characteristics, reducing the occurrence of cracks and spalling, thus extending their service life.
4. High abrasion resistance: Their structure is dense and the hardness is relatively high, and they can maintain good abrasion resistance even at high temperatures. For kilns where there are situations such as material scouring and friction during the production process, such as cement rotary kilns and ore roasting furnaces, refractory castables can resist the abrasion of materials, reduce material loss, and maintain the normal operation of the equipment.
5. Good corrosion resistance: They have a certain resistance to various corrosive media, such as furnace slag, molten metals, and corrosive gases. Certain substances in their composition will form a dense protective film at high temperatures to prevent the penetration of corrosive media and chemical reactions, improving the service life of refractory castables in harsh environments.
6. Good integrity: After casting and forming, they form a whole with no joints or very few joints. This can effectively avoid problems such as heat leakage and gas channeling caused by joints, improving the sealing and thermal insulation performance of the kiln, reducing heat loss, and also enhancing the structural stability.
7. Strong repairability: During the usage process, if there is local damage, local repair can be carried out, instead of having to replace the whole as with some shaped refractory materials. This reduces the maintenance cost and the downtime of the equipment, improving production efficiency.