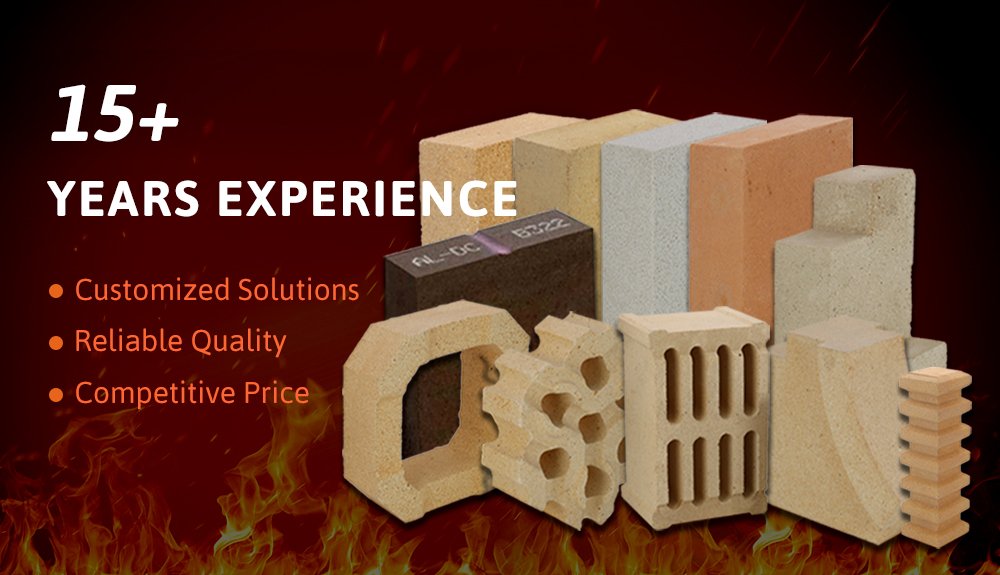
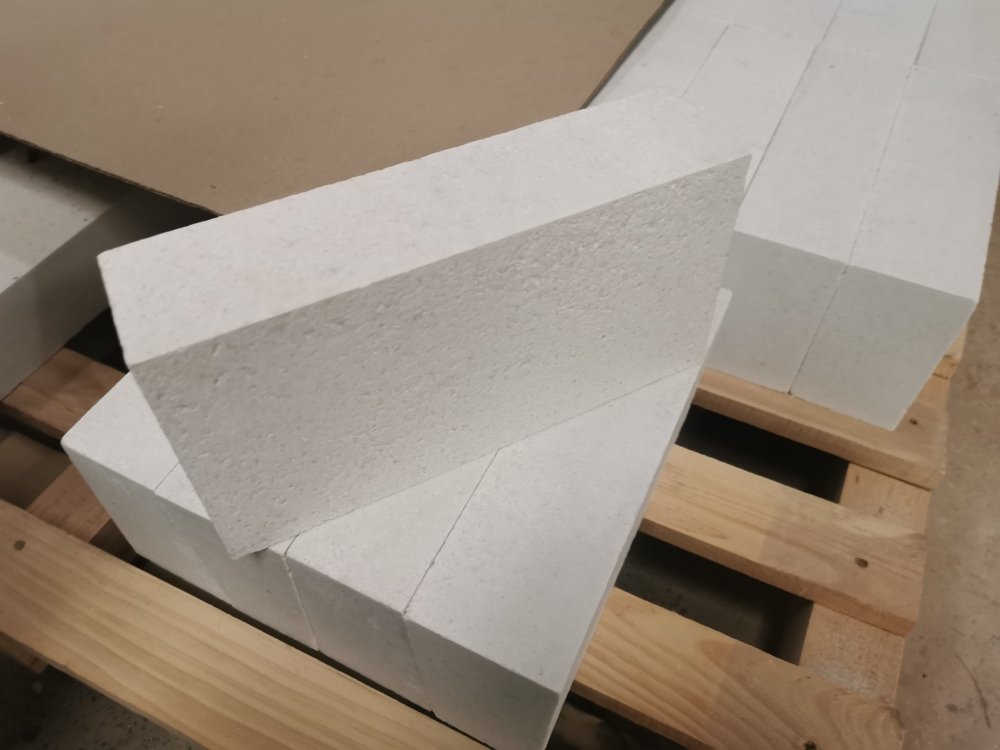
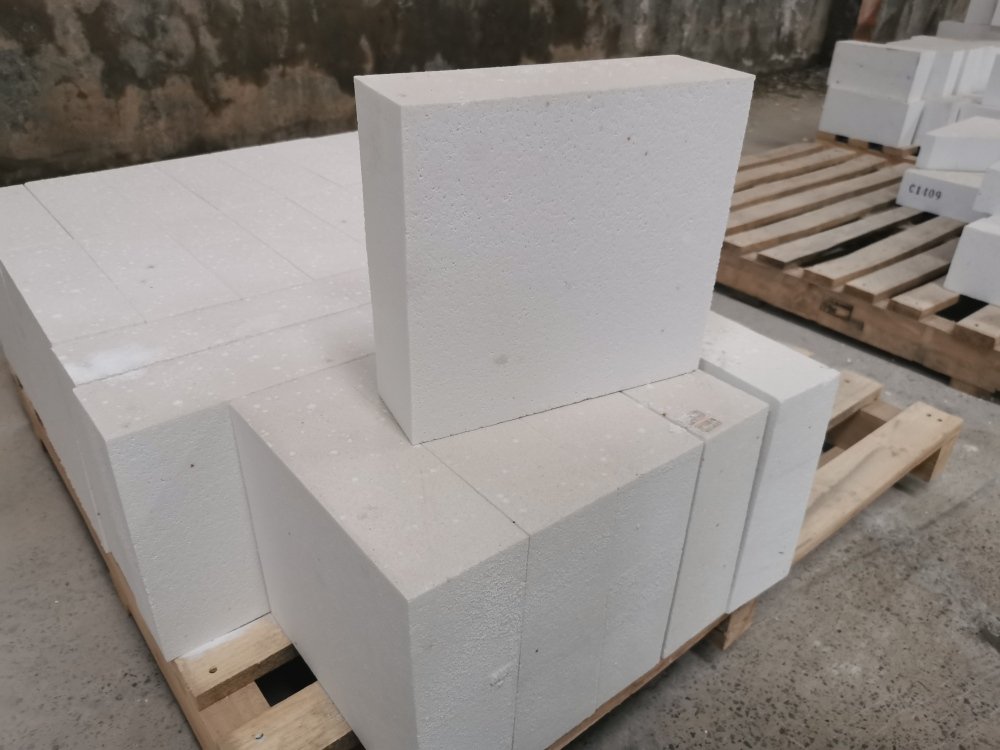
The uniqueness of corundum bricks is mainly reflected in the following aspects:
1. High Purity and Excellent Performance: Corundum bricks are mainly made of high-purity aluminum oxide, with the aluminum oxide content usually exceeding 90%, and in some cases, it can even reach 99%. This high-purity composition endows corundum bricks with a series of excellent properties, such as high hardness, high melting point, and high abrasion resistance, enabling them to maintain good performance in harsh environments like high temperatures and severe abrasion.
2. Outstanding High-Temperature Resistance: Corundum has a very high melting point (approximately 2050℃). Therefore, corundum bricks possess remarkable high-temperature resistance and can withstand temperatures of 1700℃ and above without softening or melting. In high-temperature industrial furnaces and other equipment, corundum bricks can operate stably for a long time, providing reliable support for the normal operation of the equipment.
3. Good Chemical Stability: Corundum bricks exhibit good stability against most chemical substances. Whether it is acidic or alkaline slag, molten metal, or other corrosive media, corundum bricks can show strong resistance and are not easily eroded or corroded. This extends the service life of the equipment and reduces maintenance costs.
4. High Abrasion Resistance: Corundum bricks have a very high hardness, with a Mohs hardness of up to 9, second only to diamond. This gives corundum bricks excellent abrasion resistance. When subjected to the scouring and friction of high-temperature materials, they can maintain the integrity of their surface, reducing wear and spalling. They are suitable for parts with severe abrasion, such as the furnace doors, furnace walls, and chutes of industrial furnaces.
5. Excellent Thermal Shock Resistance: Although corundum bricks have good stability at high temperatures, in practical applications, the equipment often undergoes frequent heating and cooling processes, which requires the material to have good thermal shock resistance. Through reasonable formulation design and production processes, corundum bricks have been endowed with good thermal shock resistance. They can withstand sudden changes in temperature without cracking or spalling, ensuring long-term use under thermal cycling conditions.